
Hollow Forging
Hollow forging, also known as closed-die forging with mandrel, is a highly sophisticated metal shaping technique that offers numerous benefits over other metal forming processes. Hollow forging is a metal-forming process that involves the utilization of a hollow die tool known as a mandrel. This innovative technology enables the production of complex geometrical shapes and hollow internal structures within metal components, surpassing the limitations of conventional forging methods.
Advantages of hollow forging:
-
Material Savings:
Hollow forging enables the creation of products with hollow internal structures, significantly reducing the amount of material required. Compared to other forging techniques, this can result in material savings ranging from 20% to 70%, depending on the product's shape and the design of the hollow structure. -
Strength and Durability:
Products produced using hollow forging exhibit exceptional durability and strength. The incorporation of hollow internal structures allows for weight reduction without compromising their structural integrity. This makes hollow forging particularly appealing in industries such as aerospace, automotive, and space exploration, bycicle and scooter industry, where the combination of strength, durability, and lightweight design is paramount. -
Improved Stiffness:
Hollow forging also offers improved product stiffness. By employing well-designed hollow structures, greater stiffness can be achieved compared to solid counterparts. This feature is crucial for components subjected to heavy loads and vibrations. -
Enhanced Energy Efficiency:
Hollow forging has the potential to reduce energy consumption compared to other metal forming processes. The utilization of a reduced material volume results in lower energy requirements for heating and processing the metal. This translates into significant energy savings throughout the manufacturing process. -
Streamlined Processes:
The incorporation of complex shapes and functionalities during hollow forging eliminates the need for additional machining and assembly processes. This streamlined approach reduces production time and costs.
The process commences by heating the metal workpiece to the desired temperature. Subsequently, the mandrel, specifically designed to match the internal cavity of the final product, is inserted into the heated metal, applying force to shape it. The material undergoes controlled deformation, taking the form of the hollow structure defined by the mandrel.
The advantages of hollow forging are manifold, making it an attractive choice in various industries.
Hollow forging technology offers compelling advantages in terms of material savings, energy efficiency, and streamlined manufacturing processes. The reduction in material usage, coupled with enhanced strength and rigidity, makes it an appealing choice for various industries. As the demand for lightweight yet robust components continues to rise, hollow forging remains at the forefront of innovative metal forming techniques.
The advantages of hollow forging depend on the specific requirements of the product, the materials and the manufacturing process. The proportion of material, energy and downstream process savings depends on the specific case and product design.
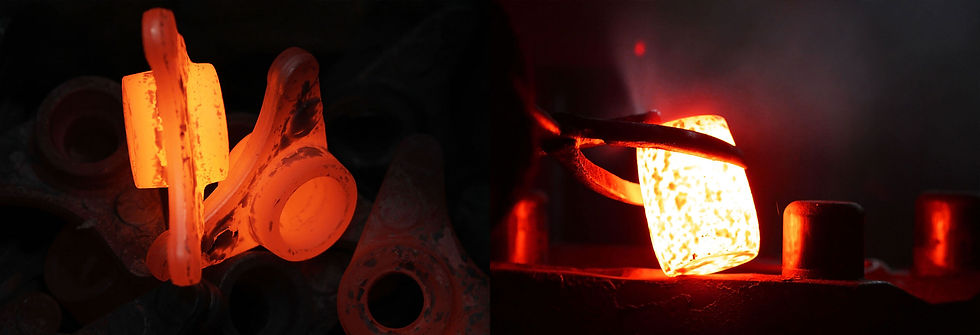